隨著國家工業生產水平逐步提升,石油產量、用量也逐年增長,同時我國石油開采技術也日趨完善[1],但由于長時間大規模開發,常規地質油井開采量不斷下降,因此國家將石油開采工作重心移向位于特殊地質環境中的油田,這類油井普遍具有超深、高溫、高壓及含硫化氫等特點[2]。例如新疆塔里木油田,油氣井多為超過4000米的深井或超深井,其溫度、壓力以及腐蝕介質含量均很高;再如西北油田,共有油氣井667口(包括油井574口,氣井93口),含H2S井470口,占總井數的70.5%,含
CO2井605口,占總井數的90.7%。由此可見,工況條件嚴苛的油氣井在石油天然氣開采中占比越來越大,井下工況愈惡劣,油氣井對油井管產品質量、可靠性、使用壽命的要求也愈發嚴格。
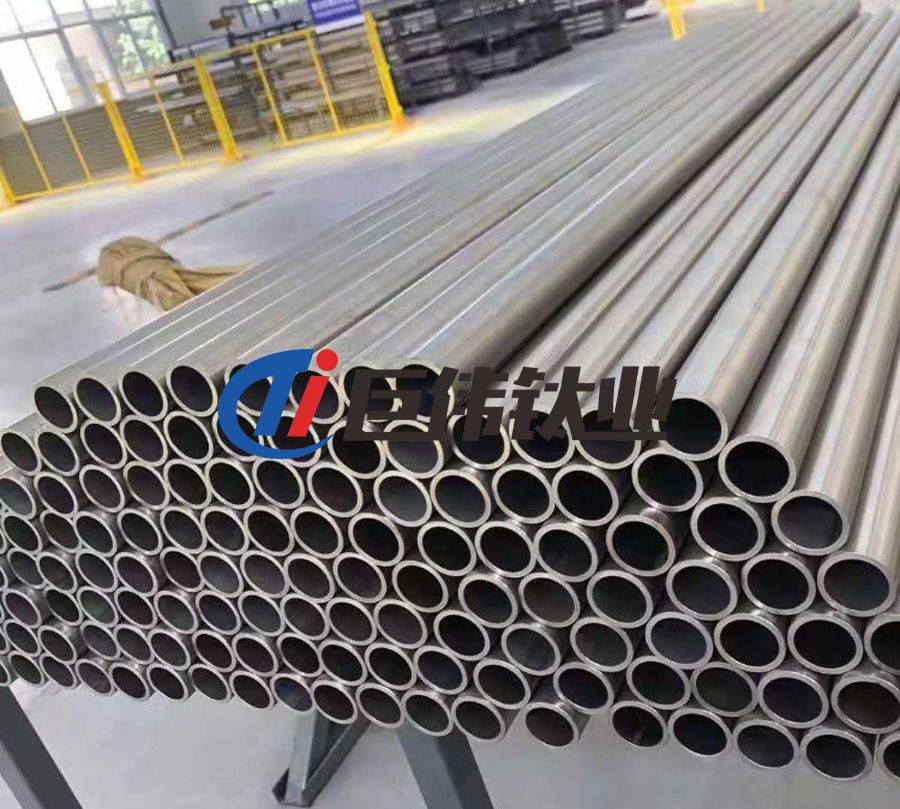
在這種行業趨勢下,鈦合金油井管憑借其優異的耐蝕性能、良好的機械性能受到業內的廣泛關注。雖然我國開展石油領域鈦合金的研究相對較晚,但隨著國家資源開發難度的增大,國內許多研究院所與管材生產企業也逐漸認識到研制鈦合金油井管的必要性和緊迫性[3],同時開展大量鈦合金耐蝕性能研究。林乃明等[4]研究了TC4鈦合金在飽和油田采出液中的電化學腐蝕行為,為拓展鈦合金在石油管方面的應用提供參考;高飛等[5]研究了Ti80鈦合金在苛刻油氣腐蝕環境中的腐蝕行為,獲取不同腐蝕環境下的耐蝕反應;梁偉等[6]模擬某油田工況,對成品TC4鈦合金無縫管材在高溫苛刻工況下的腐蝕行為進行研究;高文平等[7]對TC4成品管進行高含H2S、CO2苛刻環境下耐蝕機理研究,均為鈦合金在石油行業的應用開發提供參考;劉強等[8]對五類油氣開采用鈦合金進行耐蝕性對比,研究結果為選材和縫隙腐蝕防治提供理論基礎。
就當前石油工業領域而言,TC4鈦合金仍是應用范圍最廣泛的牌號之一,通常情況下國內無縫管生產企業也將其作為鈦合金油井管生產坯料。針對這一情況,本文開展不同牌號鈦材耐蝕性能對比試驗研究,對不同工況下鈦合金油井管坯料選擇提供理論依據,指導生產廠家材料選型。
1、試驗材料及方法
依據肖國章等[9]的研究,結合前期鈦合金市場供應情況調研結果,在充分考慮坯料購置單價經濟性的前提下,從當前石油天然氣行業可選鈦合金牌號中分別確定α型TA2、近α型TA10、α+β型TC4及TC4ELI四類材料。其中TA2為工業純鈦,TA10為鉬鎳鈦合金,TC4ELI是在TC4的基礎上降低合金中雜質元素與間隙元素含量。需要說明的是,β型鈦合金可以油管用鈦合金管、套管生產,但市場受單價限制,導致廠家供應量、用戶需求量較少,雖然其理化特性優越,卻因管材產品成本高而失去競爭優勢。本文所選四類鈦材化學成分如表1。
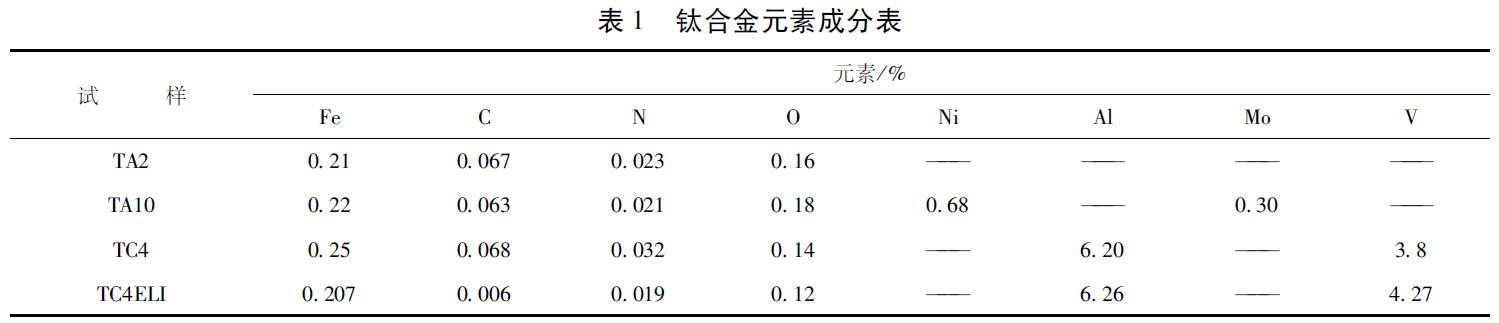
試驗采用直徑φ10mm、厚度3mm圓柱試樣,截取自生產于同一廠家40mm棒材。用環氧樹脂包裝,不同金相砂紙逐級打磨至表面光亮后選擇無水乙醇和去離子水清洗。為更準確地模擬油田實際工況下、判斷鈦材的耐蝕性能,配制同時含有Cl-、CO2、H2S腐蝕元素的模擬環境:飽和CO2的3.5%NaCl+Na2S溶液,Na2S含量0.4%,可產生H2S腐蝕效果[10]。針對油田井下溫度復雜這一特點,對模擬環境溫度進行區分,I組腐蝕環境溫度為室溫狀態(25℃),II組為加熱狀態(80℃)。測試采用傳統三電極體系,如圖1。飽和Ag/AgCl作為參比電極,鉑電極作為輔助電極,不同類型鈦材試樣作為工作電極。首先進行開路電位(OCP)測試,極化曲線測試電壓范圍為OCP±0.3V,掃描速率為0.0005V/S,電化學阻抗測試頻率范圍為10-2~105Hz,交流信號幅值為±5mV。同時對材料進行為期30天的浸泡腐蝕,環境同電化學試驗相同,并通過JSM-7001F熱場發射掃描電子顯微鏡觀察腐蝕后形貌。
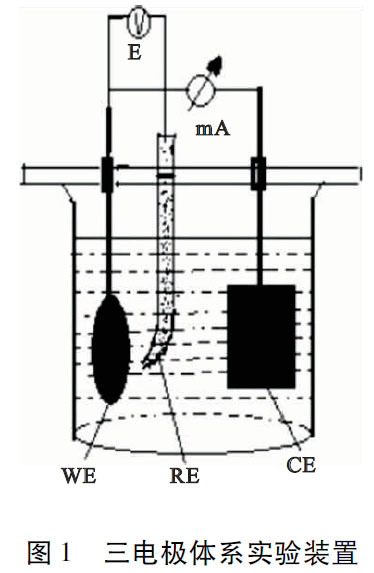
2、試驗分析及結果討論
2.1 室溫狀態測試結果分析
鈦的電化學腐蝕本質是鈦離子在電流作用下子從金屬本體轉移至環境介質中,同時伴隨著介質中氫離子吸收電子的發生,常規表現為縫隙腐蝕、點蝕等。開路電位是在穩定環境中測量無外加電流時,材料與參考電極腐蝕微電位之間的總電位差,其正負可判斷材料腐蝕傾向。室溫下四類鈦材開路電位曲線如圖2(a),OCP值均呈現由負變正且最終趨于
平穩的趨勢。測試穩定后,TA2開路電位最正,穩定在-355mV附近,TC4與TC4ELI曲線較為接近,但TC4終值約為-4498mV,TC4ELI稍負,最終穩定在-513mV附近,TA10開路電位最負,大約在-6610mV。由于合金元素分布情況在α相和β相中的含量不同,使兩相間之存在一定電位差,導致微電偶腐蝕發生的幾率較大,因此在室溫條件下,具有單相組織的TA2純鈦表現出更優異的抗腐蝕性。
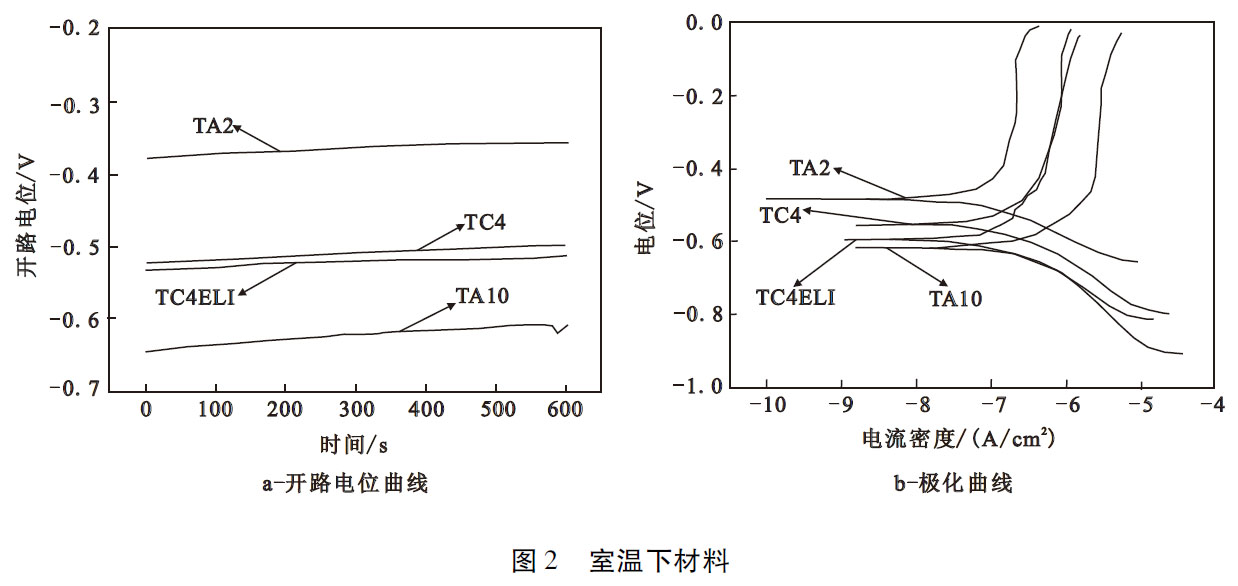
極化曲線表征腐蝕原電池反應的推動力電位和反應速度電流之間的函數關系[11]。圖2(b)中室溫腐蝕時四類材料的極化曲線整體形態相似,均存在典型的鈍化特征。這是因為鈦材表面與介質溶液反應形成一層TiO2薄膜,起到一定降低金屬溶解速度的作用,這類鈍化膜對于長期處于高溫高壓腐蝕環境中的油井管具有良好的保護作用。
表2為擬合得到的Tafel常數表,腐蝕熱力學中,自腐蝕電流密度低的材料抗腐蝕性能越優異[12],圖中TA2鈍化較早且自腐蝕電位明顯高于其它材料,值為-0.483V,自腐蝕電流密度為7.345e-8A·Cm-2,數值最小且比其他材料的ICOrr低一數量級;TA10鈦合金自腐蝕電流密度為最大,兩類TC4鈦合金介于TA2與TA10之間。擬合結果對應的耐蝕性能由強到弱依次為TA2、TC4、TC4ELI、TA10。
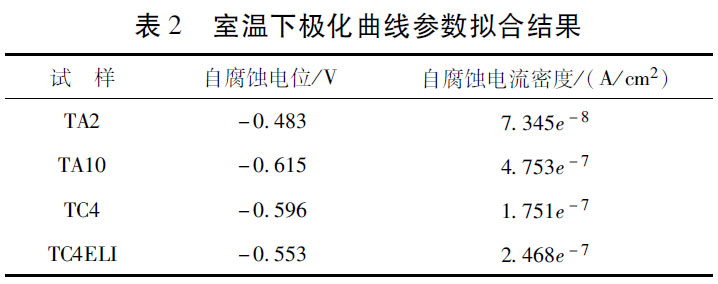
電化學阻抗(EIS)的測試原理是采用一系列小幅度正弦波或電流為擾動信號去刺激腐蝕體系,根據反饋信號推測該體系溶液電阻、極化電阻等情況[13]。圖3為室溫腐蝕時電化學阻抗譜及等效電路圖,圖3(a)中四種材料表現出相似的圖譜特征,均為單一容抗弧,但弧線之間半徑差別較大;在電極反應中,表面反應受電極電位E的影響,容抗弧半徑代表反應中所受阻力的大小,圖中四條曲線半徑由上到下依次減小,說明試驗鈦材的耐蝕能力按此順序依次降低。
利用Zview軟件進行等效電路擬合,得到電化學參數如表3。
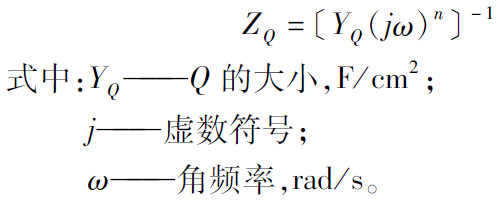
其中Q為常相位元件,其阻抗ZQ為:表中參數n為彌散系數,RS為溶液電阻,Rt為電荷轉移電阻,RS相對于Rt數值很小,所以Rt便作為評判腐蝕反應的主要依據,其值越高代表電荷轉移越難發生,材料耐蝕性能越優異[14-16]。按照以上規律,TA2電荷轉移電阻數值最大,TA10電阻最小,說明試樣TA2耐蝕性最強,TA10耐蝕性最弱,兩類TC4性能居中,阻抗譜體現的耐蝕性規律與極化曲線相同。
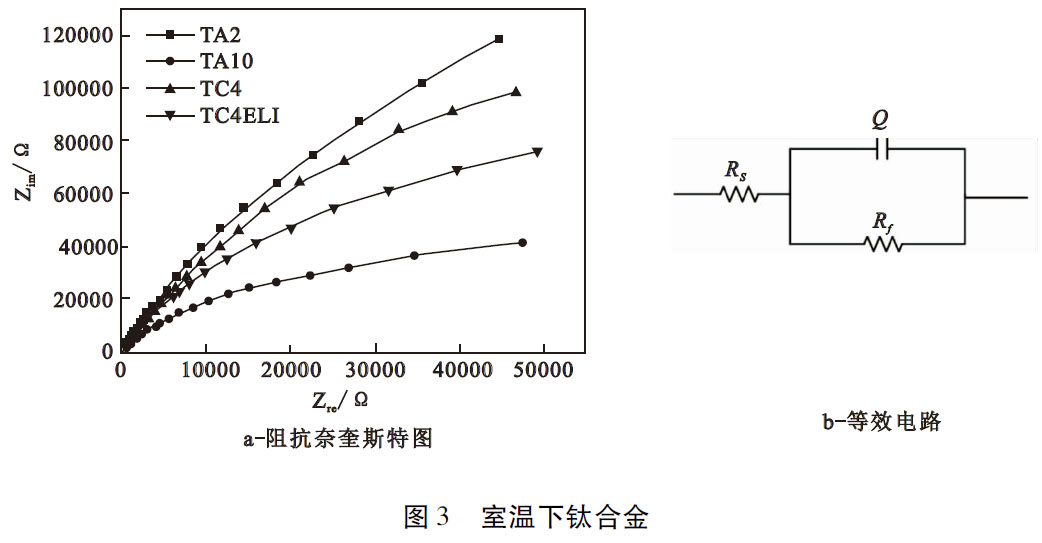
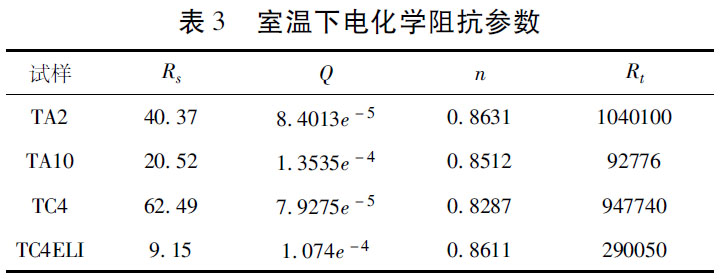
綜合得出,室溫下相同腐蝕環境中的四類鈦材具有不同的耐蝕表現。TA2作為工業純鈦,具有單一α相,單相組織因不易組成腐蝕原電池而比其余三類合金材料具有更好的耐蝕性;近α型TA10合金,包含MO與Ni元素,MO為同晶型β穩定元素,Ni為共析型β穩定元素,TC4與TC4ELI中含有α穩定元素Al元素與同晶型β穩定元素V。因此,相組成、合金元素種類及其含量的不同是導致耐蝕性能不同的根本原因。
2.2 加熱狀態測試結果分析
為準確甄別鈦材不同工況的耐蝕性能,對腐蝕環境進行加熱(80℃),此時其腐蝕性增強。因為環境溫度升高后,介質中氧擴散系數增大,同時水的黏度降低,溶液導電率增加,腐蝕電流增大。圖4為加熱狀態下開路電位與極化曲線。
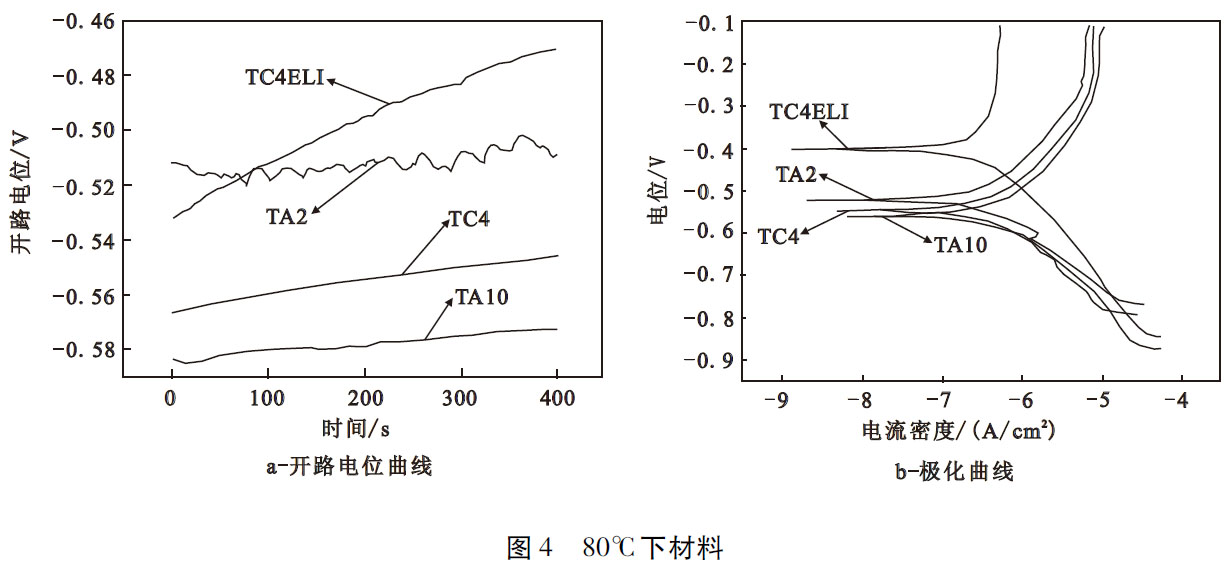
與常溫時相比,雖然OCP曲線最終趨于穩定,但過程中曲線斜率均有所增加,表明材料與介質的反應變得強烈;TC4ELI的電位區間跨度較大,測試開始時電位值約為-530mV,結束時約為-470mV,這是由于與環境接觸后合金被快速氧化積聚大量電荷,同時表面有腐蝕產物產生并形成鈍化膜導致穩定推遲;TA2曲線在整個測試過程中波動較大,反應劇烈呈現鋸齒狀,可能是由于測試系統不穩定,但數值波動范圍較小,始終在-510mV左右波動,不影響測試準確性與后續分析;TC4與TA10的曲線變化規律相似,區間跨度也較小,測試結束時,TC4鈦合金最終穩定在-550mV附近,TA10穩定在-572mV附近。
圖4(b)為環境加熱狀態下的材料極化曲線。當環境溫度升高時極化曲線分布與開路電位情況類似,均有一定變化,但曲線整體走勢和形態相同,依然存在明顯鈍化區域,擬合得到電化學參數具體如表4。同表2相比,高溫狀態的ICOrr均有一定增大,說明材料在此溫度環境比常溫時敏感,高溫腐蝕介質對鈦材的溶解更嚴重[17]。
表內數據顯示的耐蝕性按TC4ELI、TA2、TC4、TA10的順序依次降低,這與室溫狀態有所區別。其中TC4ELI在加熱狀態耐蝕性優于其他材料,可能是源于間隙元素和雜質元素的含量有所降低,這些元素與鈦原子的作用嚴重影響材料內部各相之間的價電子結構,同時對材料晶格產生影響甚至會出現內應力,從而影響系統穩定性與宏觀理化性能,如耐腐蝕性、斷裂韌性等,但這些元素的具體作用原理和影響還需后期進一步研究確定。
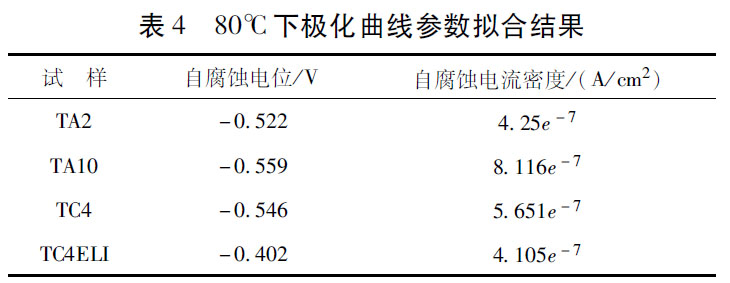
圖5為鈦合金在加熱腐蝕環境中的阻抗譜,雖然與室溫下阻抗譜有相似的單一容抗弧圖譜特征,但曲線峰值頂點卻比室溫狀態時有不同程度的降低。容抗弧半徑由大到小依次為TC4ELI、TA2、TC4、TA10。再次說明高溫腐蝕環境中的鈦及鈦合金容易進行電荷傳輸,對介質的抵抗能力更弱。
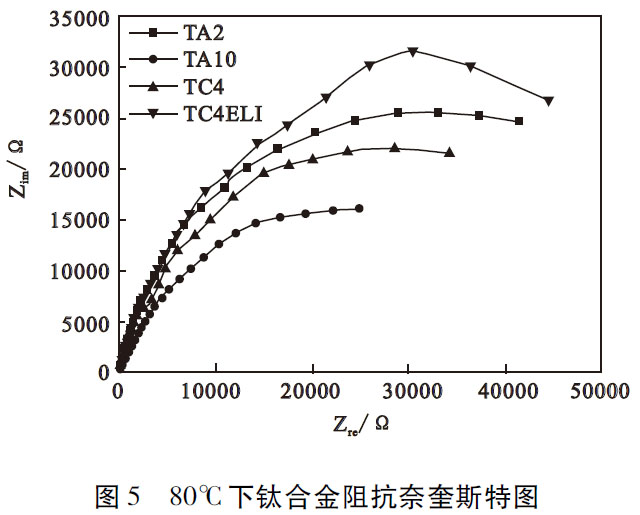
容抗弧阻抗特性類似,因此等效電路也可參照圖3(b)。擬合參數表5中電荷轉移電阻值最大的鈦材是TC4ELI,為93,617Ω·Cm2。通過與表3對比可以看出,TA2的Rt減小幅度最大,TA10減小幅度最小,說明單一α相組織的工業純鈦對環境溫度更敏感,耐蝕性能受到的影響更大,而含MO、Ni合金元素的近α相鈦合金雖然性能上稍遜于其他材料,但其耐蝕性對溫度變化的反應比較遲鈍,因為MO元素有利于β相的形成,同時改善α與β相的原子結合強度,因此可將TA10應用于溫差范圍較大、溫度變化程度劇烈的工況環境。
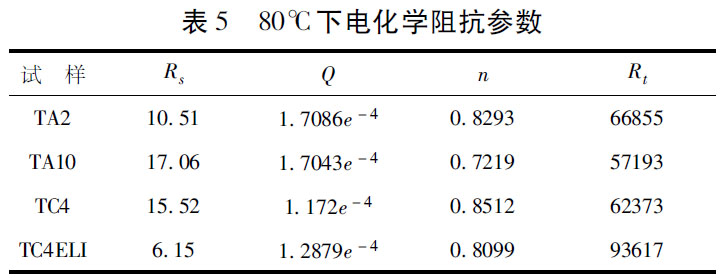
2.3 浸泡腐蝕試驗形貌
將材料浸泡置在腐蝕環境中30天,介質環境同樣分為室溫與加熱兩種狀態。圖6、圖7分別為完成浸泡之后SEM下腐蝕形貌。
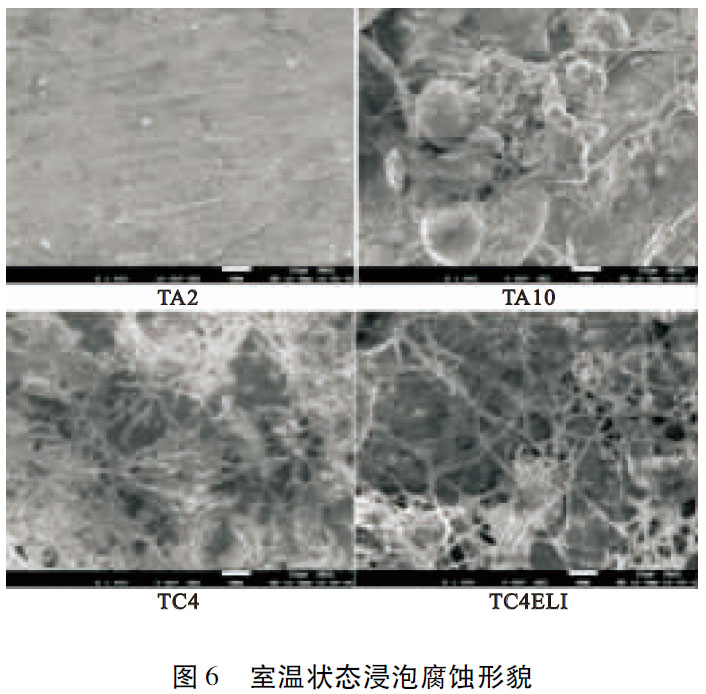
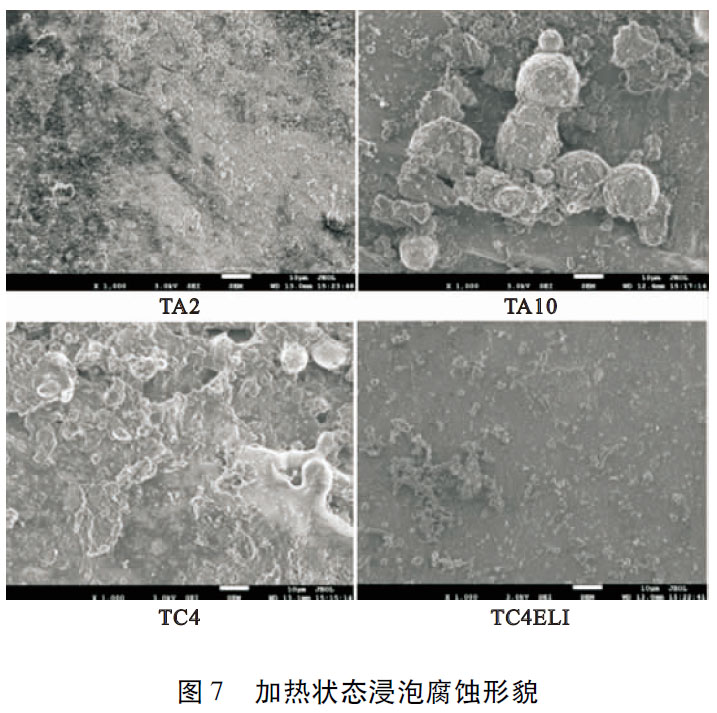
圖6中浸泡腐蝕后的TA2雖然已經失去原有光澤,但是均勻腐蝕程度輕微,表面相對平整光滑,尚未出現明顯點蝕,且總體腐蝕程度在四種材料中最輕;TC4與TC4ELI腐蝕狀態接近,已經有明顯化學反應發生,表面均出現大量不規則的絮狀腐蝕產物,同時呈現越來越疏松的趨勢,但TC4的腐蝕相對較輕。TA10鈦合金粗糙程度高,說明其與腐蝕介質的反應最強烈,溶解程度也比其余三類鈦材嚴重。
圖7所示高溫腐蝕狀態下的鈦材形貌,與室溫狀態相比,所有材料腐蝕程度均更加嚴重。TC4ELI表面出現較為密集的腐蝕坑,但都非常細微;TA2的情況類似但稍有加重;TC4與TA10材料的腐蝕產物明顯增多,分布更加廣泛并且導致材料表面凹凸不平;TC4腐蝕形成的沉淀物連續、致密,但表面積小;TA10表面附著的腐蝕產物形狀多呈現塊狀凸起,形狀、大小均更加明顯。對比發現,兩組試驗所獲取的形貌狀態與電化學參數代表的耐蝕性能結果一致。
3、結論
(1)在室溫實驗條件下,通過開路電位、自腐蝕電流密度及交流阻抗對比可知,耐腐性能TA2>TC4>TC4ELI>TA10。如果工況環境為室溫或接近室溫,工業純鈦TA2可作為較理想的坯料選擇對象。
(2)當工況環境溫度升至高溫情況時,四類鈦材耐蝕性依次為TC4ELI>TA2>TC4>TA10。通常情況下,由于油氣井下工況條件多為高溫高壓腐蝕環境,此時選材可參照80℃下腐蝕性對比結果,即優先考慮TC4ELI作為坯料材質。
(3)本論文所涉及的四類常規鈦材均具有優越的耐腐蝕性能,但在CO2-H2S-Cl--H2O環境下耐蝕性強弱排序與環境溫度有關,并非只有唯一確定的順序關系。數據表明,對于TC4鈦合金而言,合金元素含量相當的情況下,低間隙元素和雜質元素的的損傷容限設計有利于減緩腐蝕趨勢,提升材料耐蝕性能。
參考文獻:
[1]劉亞旭,李鶴林,杜偉,等.石油管及裝備材料科技工作的進展與展望[J].石油管材與儀器,2021,7(1):1-5.
[2]稅蕾蕾,蘇金長,陳金定,等.高溫高壓油氣藏開發實驗技術研究進展[J].石化技術,2017,24(6):141-142.
[3]蔣偉,趙金平,龔敏.鈦及鈦合金在防腐應用中的研究現狀和前景[J].輕金屬,2007(9):59-63.
[4]林乃明,鄒嬌娟,王振霞,等,唐賓.熱氧化TC4合金在CO2飽和模擬油田采出液中的電化學腐蝕行為[J].稀有金屬材料與工程,2018,47(1):274-278.
[5]高飛.苛刻腐蝕環境中鈦合金油套管材料的適用性研究[D].西安:西安石油大學,2020.
[6]梁偉,謝俊峰,王雅倩,等.苛刻工況條件下鈦合金管材的腐蝕電化學特性研究[J].熱加工工藝,2018,47(6):98-102.
[7]高文平.高含H2S/CO2苛刻環境鈦合金管材的耐蝕機理研究[D].西安:西安石油大學,2017.
[8]劉強,惠松驍,汪鵬勃,葉文君,于洋,宋生印.油氣開采用鈦合金石油管材料耐腐蝕性能研究[J].稀有金屬材料與工程,2020,49(4):1427-1436.
[9]肖國章.鈦合金油井管的生產加工工藝研發現狀[J].鋼管,2018,47(2):9-15.
[10]尹志福,朱世東,南蓓蓓,等.2205雙相不銹鋼在CO2-H2SCl--H2O環境中的電化學腐蝕行為[J].材料保護,2016,49(3):23-26+7.
[11]林玉珍,楊德鈞.腐蝕和腐蝕控制原理[M].北京:中國石化出版社,2007.
[12]高飛.苛刻腐蝕環境中鈦合金油套管材料的適用性研究[D].西安:西安石油大學,2020.
[13]余存燁.耐蝕鈦合金的發展[J].鈦工業進展,2003(1):12-19.
[14]喬巖欣,任愛,劉飛華.690合金在NaCl溶液中的電化學行為研究[J].中國腐蝕與防護學報,2012,32(2):146-150.
[15]曹楚南.電化學腐蝕原理[M].北京:化學工業出版社,2008.[16]楊明.H2S/CO2條件下油井管選材研究[D].北京:中國石油大學,2018.
[17]羅強,王理,陳新,等.TA16和TA17鈦合金在高溫高壓水中的腐蝕行為研究[J].輕金屬,2012(2):56-59.
相關鏈接